Machine tools Precise speed and position detection with bearingless encoders
Electric drives keep your machines moving! Our sensors supply valuable information in real time for the control and intelligent condition monitoring of your electric motors in highly dynamic, high-precision applications. We use efficient, time-optimised algorithms to process sensor measurement data in the smart sensors synchronously with the running time of the processes.
Our MiniCODERs are globally the most frequently used encoder kits in the high-speed spindles of machine tools. More than 500,000 of these bearingless encoders are already in use in high-speed cutting, power cutting and high-precision milling and grinding machines.
Based on integrated microprocessors, the new MiniCODER generation sets new standards in communication and data preparation. Why not see the benefits of our system solutions for yourself?
i³SAAC
We believe that our systems will increasingly be able to analyse and evaluate data independently with the aid of artificial intelligence (AI) and other forms of “data analytics” in the sensor. This will enable them to respond to changes in external influences and optimise themselves autonomously based on information exchanged between the components of your machine.
In future trained sensor systems will be able to act independently and to identify and actively report possible damage at an early stage, preventing expensive standstills. What it means for you is that your machines will become more efficient. This allows true preventative maintenance as a function of the condition of the machine and ensures permanently high availability.
We are already making use of the analytics of AI by training applications under real-life conditions. You know your application, we analyse the sensor data and obtain findings.
High signal quality in operation
The parameters of your machine change subtly in operation. In encoder kits, for instance, this has an effect on the air gap between the target wheel and the sensor. Our intelligent sensors compensate for slight deviations in the signals. Active distance monitoring ensures you always get the necessary signal quality of the sensor system. By analysing the data, you can also detect critical situations such as bearing damage or damage to the target wheel at an early stage.
Signals for efficient drives
Control the drives of your highly dynamic machine efficiently and independently of the chosen control system or the motor feedback system used. Our intelligent MiniCODERs supply the appropriate speed signals and information.
Would you like to acquire the speed and position of your CNC drives? Choose features from our modular MiniCODER system such as output signal, target wheel module, design and interface and assemble your own bearing-less encoder kit.
You can parametrise the position and speed sensor after installing it in your machine, enabling you to adapt the complete system optimally to your application.
Do you have to acquire the rotor position in your drive with a high degree of positioning accuracy? Thanks to the vernier analysis, the precise rotor angle is available to you immediately after the absolute encoder kit is switched on – with no need to rotate the shaft. Your feedback system receives the angle position in high resolution.
You can also use the speed signals of the single or multiturn encoder and control the torque of your motor with a sensor.
Condition monitoring
Prevent failures by monitoring the condition of your machine at all times. Our systems enable us to reduce the enormous flood of data and support efficient condition monitoring through prepared information. Our MiniCODERs acquire the temperature, vibrations and running time in addition to the speed. The encoder kits can output status or warning messages directly if limit values that can be configured or trained are exceeded.
Our software solutions make it possible in principle to also monitor the drives/spindles through remote maintenance. Further software functions such as speed histograms make the operating behaviour of your machine more transparent and offer potential for process optimisation. Use our intelligent measuring systems for comprehensive condition monitoring.
Integration into your system architecture
Choose the right interface for your machine park and integrate our products into your system architecture. Connect the MiniCODER with SSI or digital interface directly to the control system without the need for a signal transformer. You can, for instance, define thresholds and early warning levels or check temperature, amplitudes and device data, profiting from prepared information. The digital interface also gives you remote access to your encoder kit, enabling you to identify malfunctions in the drive at an early stage.
Our system solution will support you with menu-led configuration and diagnostic functions in assembly and service operations. We help you analyse the sensor data with an intuitive web browser interface, enabling you to monitor the run-in program of your spindles, for instance, without the need for additional temperature sensors. You can increase signal quality simply by adjusting the sensor signals of the integrated encoder. Use our service tool GEL 211 to transfer the measurement data of the MiniCODER to your database. Save your service reports and document the machine data efficiently and conveniently.
Bearingless encoders and target wheels
Individual MiniCODER support
Can’t find a suitable MiniCODER for your application? We manufacture sensor types in many customer-specific variants. Our technical support team will be happy to advise you. Contact us now!
*Mandatory field
Your contact
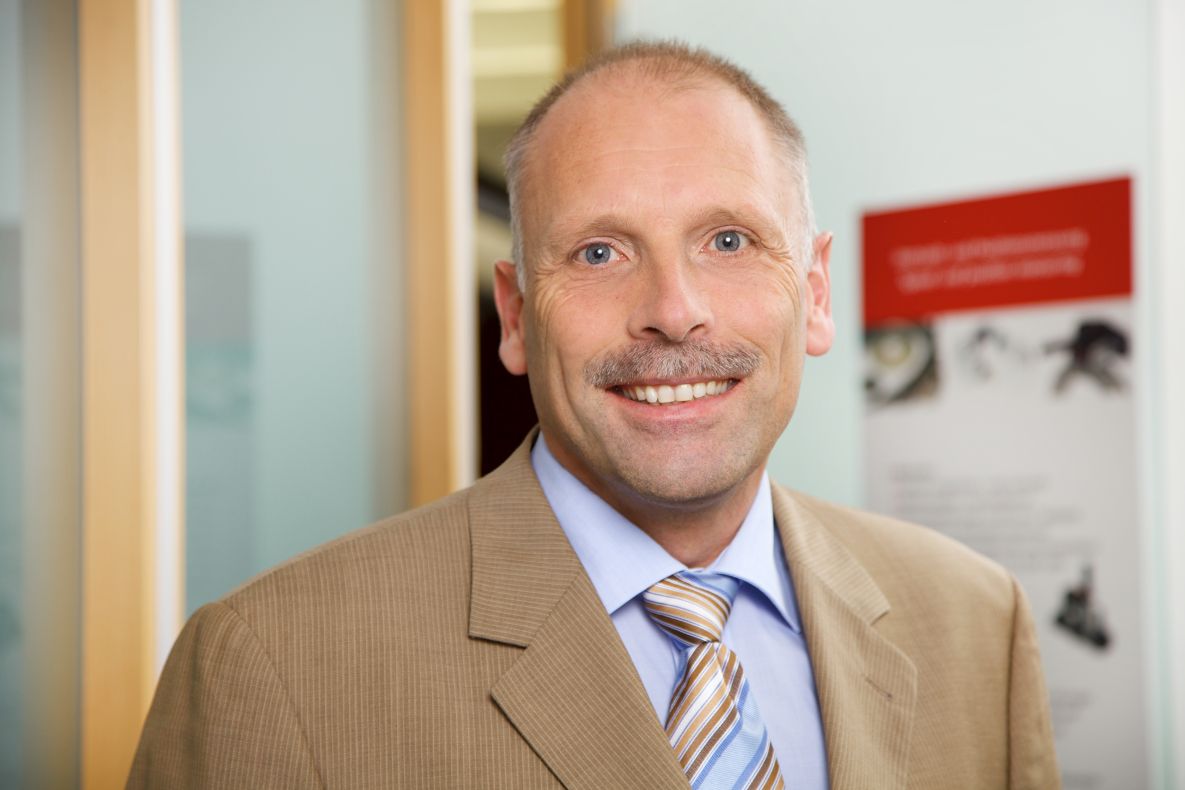
Ralf Luthmann, Key Account Manager