New analysis options in guarantee and service cases
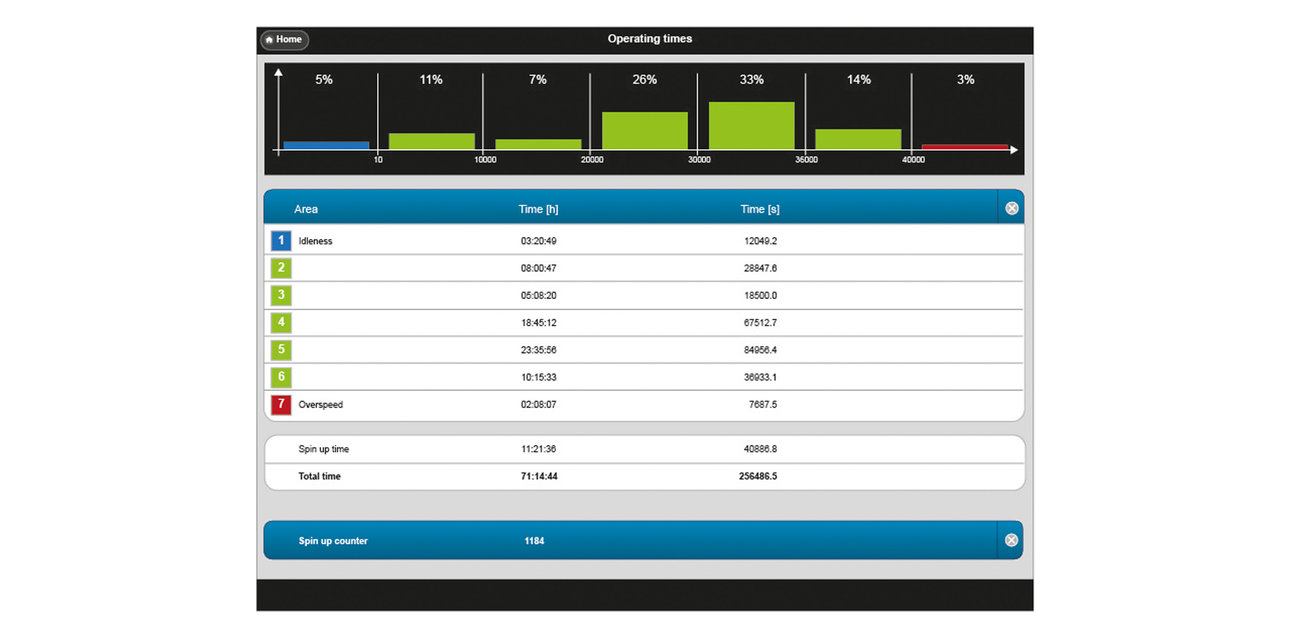
Intelligent sensors can do more than simply acquire rotational speeds: in the i³SAAC MiniCODER, the operating hours can be configured to the rated speed of the motor spindle as a speed histogram. The stored data opens up analysis options in guarantee and service cases. They supply information about the actual operating speeds and hence the loads on bearings. The OEMs of the motor spindles can use this field data to evaluate possible causes of failure in more detail and optimise the spindles to the particular application. Users will ultimately profit from greater reliability and availability and lower service costs.
Spindle servicing is often handled through third-party providers. The electronic rating plate allows the right i³SAAC MiniCODER to be detected automatically. Installation of the sensor and target wheel is documented by fine tuning in the installed state and the fingerprint of the system. This data can also be used in order to determine the optimum time for the maintenance service, allowing the replacement of spindle components to be scheduled to fit in with continuing production.
The end effect is more production time, lower repair costs and long-term protection for machine tool spindles. Intelligent sensors enable the expert data analysis knowledge of the sensor manufacturer to flow into comprehensive condition monitoring and sustainably support process optimisation.