Smart system for positioning applications
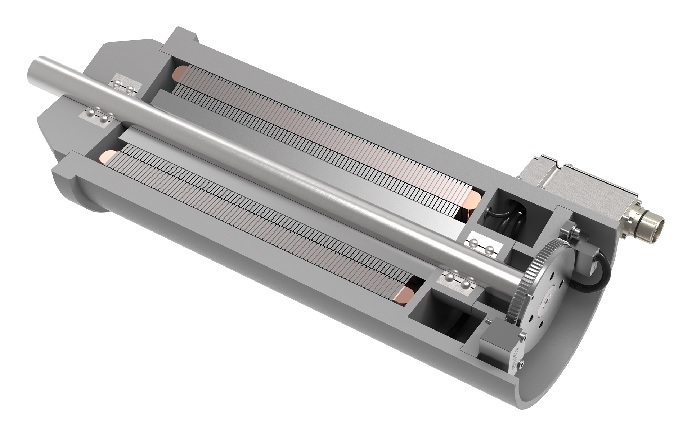
In future, identical Lenord+Bauer encoder kit types can be used in machine tools in other applications such as swivel axis and rotary table, as a double-head variant for high-precision positioning applications, which are often already in use as a single solution for rotational speed measurement. This significantly reduces the number of variants, and the existing MiniCODER high-speed solutions are retained.
If the position of an axle is to be measured exactly, measuring scales must be fitted with enormous precision. Supporting sensor solutions have so far been difficult to integrate. The easy to mount Precision-System now solves this problem. It consists of two tried-and-tested standard MiniCODERs and the Precision-Box for direct spindle mounting and the target wheels produced by the hobbing process.
Rotary tables are now usually equipped with angle measurement systems, which are very costly as a housed variant. Optical systems are frequently used as encoder kit systems, which can be contaminated in the harsh environment of the machine tool. The Precision-System offers a proven robust sensor technology for this application at a competitive price.
In spindle applications, precise speed control is mandatory not only at high speeds but also at low speeds, for example when cutting thread. The Precision-Box is connected by means of a compact connector solution using two encoder kits mounted offset at an angle of 180° on the target wheel. There is usually no need for design changes: The bearing flange just needs to be slightly adapted with the identical, 180° offset boring and milling sketch of the MiniCODER.
The analogue signals they produce are processed and prepared in the box. This dynamically minimises the eccentricity error - also known as the long-wave error - even at high rotational speeds up to well over 50,000 rpm. Temperature signals from the spindle can likewise be connected in the box and looped through in a cable for further processing.
The encoder kits can be configured using the GEL 211CSO testing and programming unit. In the installed state, the two sensor signals are finely adjusted once under menu guidance using the commissioning wizard.
The achievable precision can be evaluated by assessing the precision of mounting and the quality of the target wheel. This allows defective measuring scales to be identified at a very early stage and excessive deviations from concentricity or the MiniCODER mounting position to be corrected.
The user profits from a precise, flexible and overall cost-optimised positioning solution with high reliability.