Single turn encoder for modern drives
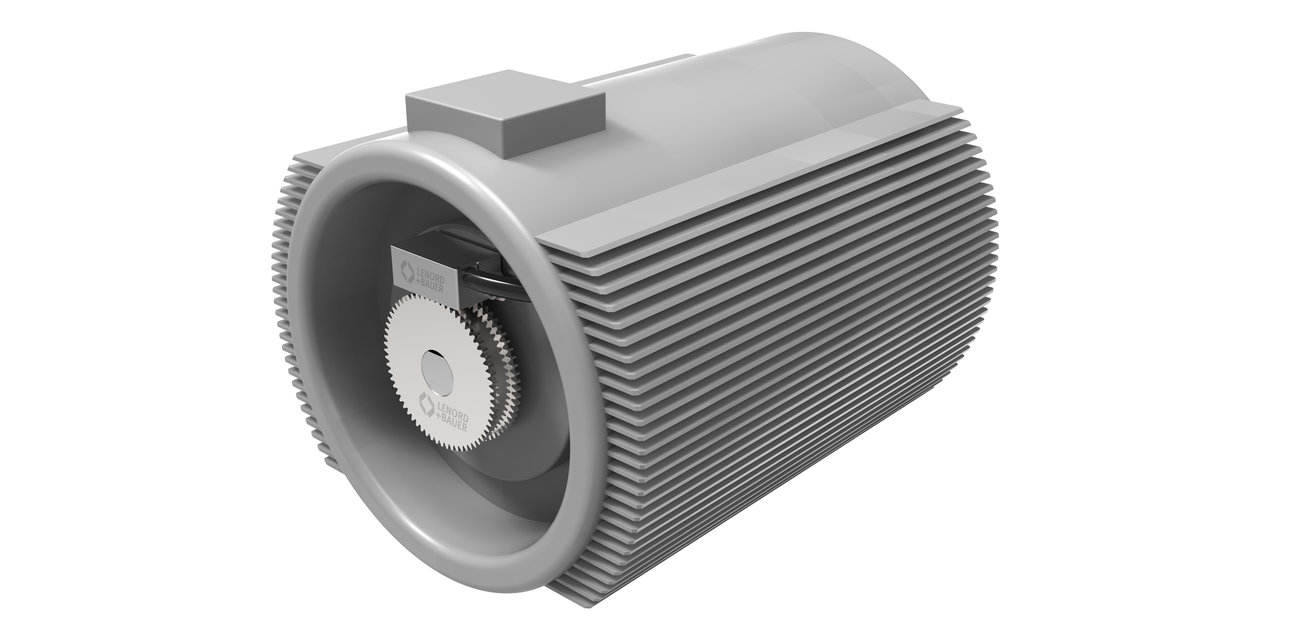
Controlling the torque of synchronous and servomotors entails acquiring the exact rotor position. On the rotor of these drives there are permanent magnets whose absolute position must be acquired at least over one pole pair range. Lenord, Bauer & Co. GmbH has developed the GEL 2800 single turn encoder kit with additional incremental output for this application. The vernier measuring system of the specialist in motion sensors and integrated drive technology consists of a scanning unit and a two-track target wheel that is mounted directly on the drive shaft. The sensor system scans the two wheel tracks of 64 and 63 teeth contactlessly and delivers two corresponding sinusoidal signals. Through interpolation, the system achieves an overall resolution of 18 bits.
The position data is transmitted by means of a serial interface. In addition, the encoder kit outputs two 90° phase-offset square-wave signals for speed acquisition. The system is adjusted to the control system and the application via parameters such as interpolation and division factor by means of a testing and programming unit. This device automatically recognises the encoder kit and supports the personnel in the configuration and commissioning of the measuring system. For commissioning, the system is connected to the testing and programming unit. It exchanges the data with a tablet or PC via WLAN or Ethernet. The data is presented in a web browser regardless of the operating system.
After installation, the scanning unit and target wheel are calibrated in the current installation situation. During this process the system compensates mechanical tolerances. The encoder corrects slight deviations in the air gap by adjusting the signal. In the consistency test, the device checks whether the output signal of the encoder kit provides only increasing or decreasing position values with the same direction of rotation. All tests are performed and the results displayed in the graphic user interface of the web browser. The service technician can document the work by saving the data in a report. This allows the measuring system to be checked fully and documented on site.