Efficient format changes
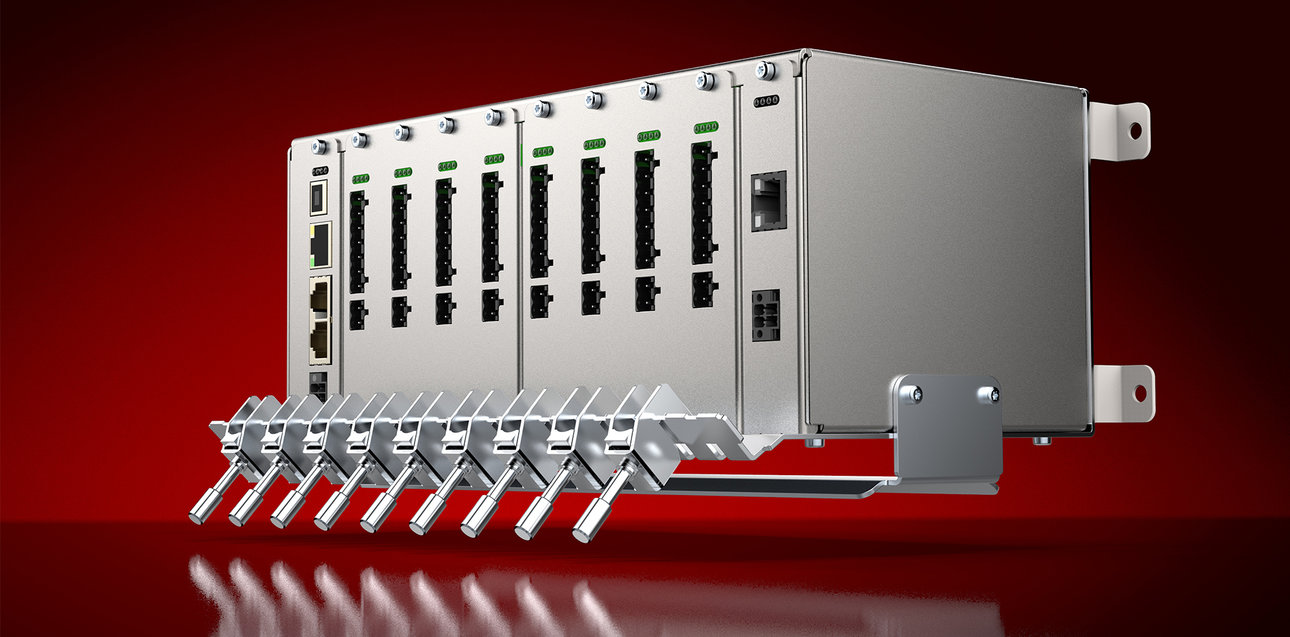
In modern packaging machines, positioning systems ensure efficient and reproducible format changes. The modular SeGMo-Box from Lenord+Bauer allows up to 17 secondary axes to be automated with intelligent positioning drives. A maximum of four boxes can be combined into a logical unit. At the heart of the modular control unit is the CPU module in the master box. What are known as COM modules ensure communication between the individual boxes with four or nine selectable module slots. Each drive is connected to a module by just one hybrid cable. The beauty of this cable is that the power supply for the motor is separate to that for the logic, which means that communication and diagnostic functions are maintained even while the motor power supply is switched off. To optimise cable lengths, the boxes can be located at a number of places across the system. Grouping positioning drives together via the configuration of the distributed boxes allows parts of a system to be switched off safely.
As a subsystem, the modular SeGMo-Box relieves the communication network of the machine and optimises the flow of data, while the CPU module, as the node, handles communication with the machine control system (PLC). The configurable Ethernet-based real-time interface supports communication profiles such as PROFINET, EtherCAT, POWERLINK, EtherNet/IP and Modbus/TCP. The proven function blocks (FBs) of the existing PowerDRIVE-Box are used to integrate the system into the machine controller. The FBs generate the traversing tasks needed in order to control the drives and forward status data such as motor current, absolute position, device temperature and thresholds to the PLC. Analysis of this device data assists in the preventative maintenance of the machine, for instance.
The CPU module can also exchange data by means of a USB port or web browser. This allows parameter sets to be written to the CPU and status data to be read and processed directly.
In the future the range of functions of the modular SeGMo-Box can be extended via optional software add-on packages.