Error-free format changing with positioning drives “Our customers purchase a high level of security from us”
Customer demands for speed, reliability, flexibility and productivity of packaging machines are constantly growing. The goal is to avoid adjustment errors and damage to products when setting up different packaging sizes.
Lantech, based in Malden in the Netherlands, builds systems in which such adjustments are carried out fully automated and with high reproducibility in the shortest possible time.
High flexibility requirements
“Our customers purchase a high level of security from us,” says Jurgen Wilbers, director of the electrical engineering department. Lantech has been active in the packaging industry since the 1970s, when it invented the pallet wrapper. The company, which employs 500 staff worldwide, offers solutions for end-of-line packaging machines. In the continuous further development of carton erectors, carton sealers, and tray and lid erectors, Lantech works closely with external partners who provide both advice and support.
When developing the carton erector, Lantech’s goal was to build a machine that was technically superior to other systems available on the market. The result: The principle used to handle cartons during the folding process ensures very high machine availability of 99.9 %.
According to Frank van Loon, Manager of R&D at Lantech, “E-commerce has led to a rapid evolution in the functionality of our carton erectors. Systems must become ever more flexible and must be suitable for processing different carton formats. 20 to 30 carton sizes are processed on a single machine.”
Originally, the necessary width and height adjustments for setup in another format were made using handwheels. For this purpose, an adjustment table was used in which the position changes per axis are described. The main disadvantage in this case is being reliant on the knowledge and skills of the machine operator, because one operator may be more accurate than another operator. Incorrect manual settings can result in damage to the product or the machine. Apart from the risk of error, the time required is also significantly higher.
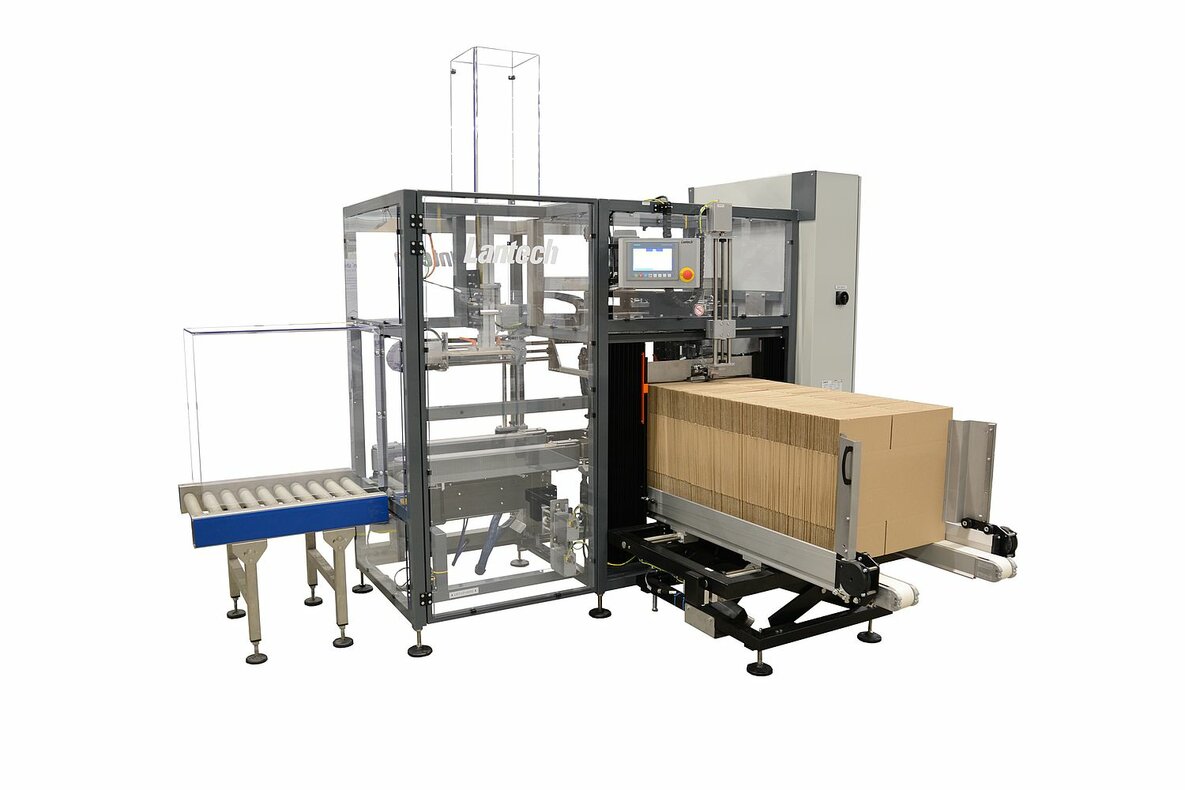
Source: Lantech
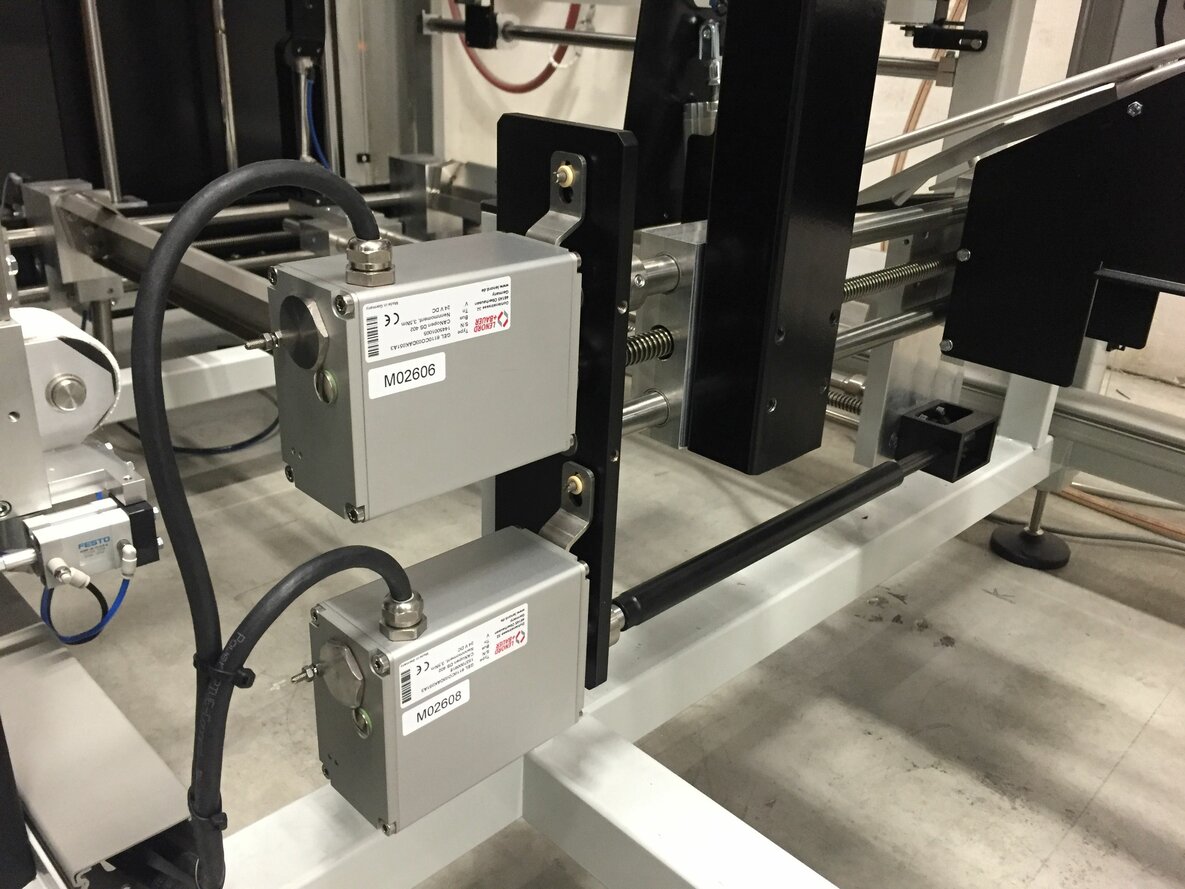
Source: Lantech
Automatic process adjustment
While further developing the carton erector and integrating automatic axis adjustment, Lantech was looking for a technology that would allow different carton sizes to be selected via the PLC touch panel. Lenord+Bauer from Oberhausen, a specialist in positioning drives and motion sensor technology, came to the rescue.
To ensure that different carton sizes can be processed perfectly, some adjustments are made in the process. The height and width settings therefore have to be adjusted both at the machine inlet and outlet. These previously manual process settings should now be fully automated and error-free.
For this purpose, each setting was automated using a Lenord+Bauer SeGMo positioning drive mounted directly on the spindle. The electrical interface to the PLC can be realized with any Ethernet-based protocol. “Lenord+Bauer offers all function blocks free of charge, for example TIA Portal and EthernetIP. This saves us a lot of programming work,” Jurgen Wilbers states. The function blocks of standard Industrial Ethernet profiles such as Profinet, EthernetIP, Ethercat, SercosIII or Powerlink are provided in the Lenord+Bauer SeGMo Library and form the basis for safe and easy drive commissioning.
A single positioning drive type is used for the various format change settings. Using a hybrid cable, which provides both power and communication, saves installation time. The positioning drives are connected via a decentralized control unit called the SeGMo-Box. Various functions can be accessed via this control unit, such as the scope function for power consumption per motor. Parameterization of motor settings can also be performed locally.
Automation of the manual settings enables fast and reliable format changes at the touch of a button. “Our machines are highly modular. We have worked out the various machine functions in detail in our engineering. Automatic format change is thus a functionality that we can easily access and use as an option for our other machines as well,” explains Jurgen Wilbers.
Industry 4.0
Further development of equipment is always progressing at Lantech: As Marketing Manager Bob Lemmen explains, “COVID-19 has made us and our customers realize that remote machine setup and process monitoring are now vital. Users want to get even more information from their machines, for example, to avoid downtimes and perform preventive maintenance on their machines.”
“In this respect, we benefit from the commitment of Lenord+Bauer. Their R&D department has thought about how to use, for example, one current consumption per axis for a safety system. If an axis consumes too much current for its intended purpose, the PLC displays an error message. This can prevent damage to products and machinery,” Jurgen Wilbers adds.
The Dutch company always has an eye on the use of new and more advanced Lenord+Bauer products. “The modular SeGMo-Box is in line with this context. It offers the possibility of remote access via a separate secure communication channel,” says Peter Lammers, Technical Sales Engineer at tsb-bescom, Lenord+Bauer’s sales partner in the Netherlands. “This system, which is now modular in contrast to the previous SeGMo-Box, enables optimum configuration depending on the number of axes to be controlled.”
In addition, Lantech has also recently started using the SeGMo-Assist digital position display for partial automation. “Our customers have differing requirements for the level of automation. We can now respond to these requirements in a flexible way,” Jurgen Wilbers states. Like the positioning drives, the digital position displays can also be connected to the modular SeGMo-Box. Thus, both can be integrated together into an Industrial Ethernet fieldbus network and managed centrally via the SeGMo-Box. This saves the user time during commissioning.